In the realm of supply chain management, there exist two crucial strategies that play a pivotal role in optimizing inventory levels and ensuring efficient operations: just-in-case (JIC) and just-in-time (JIT). These approaches, while sharing similarities, exhibit distinct characteristics and applicability in different business environments.
Just-in-case (JIC) is a traditional strategy that prioritizes maintaining a safety stock of inventory to buffer against uncertain demand fluctuations and potential supply disruptions. This approach aims to minimize the risk of stockouts and ensure uninterrupted production or customer fulfillment by holding additional inventory beyond the immediate requirements. The primary objective of JIC is to safeguard against unforeseen contingencies and maintain a high level of service.
In contrast, just-in-time (JIT) is a lean production methodology that seeks to eliminate waste and improve efficiency by minimizing inventory levels and producing goods only when customer demand materializes. This approach relies on precise coordination and collaboration among suppliers, manufacturers, and distributors to ensure a seamless flow of materials and finished goods. The core principle of JIT is to reduce lead times, minimize costs associated with carrying inventory, and enhance responsiveness to changing market conditions.
Just-in-Case and Just-in-Time
These two inventory management strategies offer distinct approaches to supply chain optimization.
- JIC: Safety Stock Buffer
- JIT: Eliminate Waste, Improve Efficiency
- JIC: Minimize Stockouts, High Service Level
- JIT: Reduce Lead Times, Lower Inventory Costs
The choice between JIC and JIT depends on factors such as demand variability, supply reliability, and the cost of carrying inventory.
JIC: Safety Stock Buffer
Just-in-case (JIC) inventory management strategy revolves around maintaining a safety stock buffer to mitigate the risks associated with demand uncertainty and supply disruptions.
- Buffer Against Uncertainty:
Safety stock acts as a cushion to absorb unexpected fluctuations in demand or unexpected supply chain disruptions, ensuring uninterrupted operations and customer satisfaction.
- Minimizing Stockouts:
By keeping extra inventory on hand, JIC aims to minimize the chances of stockouts, which can lead to lost sales, customer dissatisfaction, and potential damage to reputation.
- Ensuring High Service Level:
Maintaining a safety stock buffer allows businesses to maintain a high level of customer service by fulfilling orders promptly and reliably, even during periods of high demand or supply constraints.
- Trade-off: Increased Carrying Costs:
Holding safety stock comes with the downside of increased carrying costs, including storage space, insurance, and capital tied up in inventory.
The effectiveness of the JIC approach hinges on accurate demand forecasting and careful monitoring of inventory levels to prevent excessive stockpiling, which can lead to obsolescence and wastage.
JIT: Eliminate Waste, Improve Efficiency
Just-in-time (JIT) inventory management strategy is predicated on the principle of eliminating waste and improving efficiency by minimizing inventory levels and producing goods only when customer demand materializes.
- Waste Elimination:
JIT aims to eliminate all forms of waste, including waste of materials, labor, and time, by optimizing production processes and minimizing non-value-added activities.
- Minimized Inventory Levels:
By producing goods only when needed, JIT keeps inventory levels to a minimum, reducing carrying costs and the risk of obsolescence.
- Improved Responsiveness:
JIT enables businesses to respond quickly to changes in customer demand by adjusting production schedules and sourcing materials as needed.
- Reduced Lead Times:
With minimal inventory, lead times are shorter, allowing for faster order fulfillment and improved customer satisfaction.
JIT's success relies on precise coordination and collaboration among suppliers, manufacturers, and distributors, as well as accurate demand forecasting and efficient production planning.
JIC: Minimize Stockouts, High Service Level
Just-in-case (JIC) inventory management strategy places a strong emphasis on minimizing stockouts and maintaining a high level of customer service. This is achieved by carrying safety stock, which acts as a buffer against unexpected fluctuations in demand or supply disruptions.
Benefits of Minimizing Stockouts:
- Preserving Customer Satisfaction: Stockouts can lead to lost sales, customer dissatisfaction, and potential damage to reputation. By minimizing stockouts, businesses can ensure that customers receive their orders promptly and reliably, fostering positive customer relationships.
- Mitigating Lost Sales: Stockouts can result in lost sales and revenue. Maintaining adequate safety stock helps businesses avoid these losses by ensuring that they have sufficient inventory to meet customer demand.
- Maintaining Market Share: In competitive markets, stockouts can lead to customers switching to competitors who can fulfill their orders. Minimizing stockouts helps businesses retain their market share by ensuring that they can meet customer demand consistently.
Challenges of Maintaining High Service Level:
- Increased Carrying Costs: Holding safety stock comes with the downside of increased carrying costs, including storage space, insurance, and capital tied up in inventory.
- Risk of Obsolescence: Safety stock can become obsolete if demand patterns change or products become outdated. This can lead to losses due to write-offs or markdowns.
- Inaccurate Demand Forecasting: The effectiveness of the JIC approach hinges on accurate demand forecasting. Inaccurate forecasts can lead to either excessive safety stock, resulting in higher carrying costs, or insufficient safety stock, increasing the risk of stockouts.
Overall, the JIC strategy is best suited for businesses operating in environments with high demand uncertainty, unpredictable supply chains, or a strong emphasis on maintaining high customer service levels.
JIT: Reduce Lead Times, Lower Inventory Costs
Just-in-time (JIT) inventory management strategy is designed to reduce lead times and lower inventory costs by minimizing inventory levels and producing goods only when customer demand materializes.
Benefits of Reducing Lead Times:
- Improved Customer Responsiveness: Shorter lead times allow businesses to respond more quickly to changes in customer demand, enabling them to deliver products and services faster and more efficiently.
- Reduced Production Costs: Shorter lead times can help reduce production costs by eliminating the need for large production batches and allowing for more frequent adjustments to production schedules based on actual demand.
- Increased Flexibility: Shorter lead times provide businesses with greater flexibility to adapt to changes in market conditions, such as fluctuations in demand or the introduction of new products.
Benefits of Lower Inventory Costs:
- Reduced Carrying Costs: By minimizing inventory levels, JIT reduces carrying costs associated with storage space, insurance, and capital tied up in inventory.
- Lower Risk of Obsolescence: With lower inventory levels, businesses are less likely to be left with obsolete products, which can lead to losses due to write-offs or markdowns.
- Improved Cash Flow: Lower inventory levels can improve cash flow by reducing the amount of capital tied up in inventory and accelerating the conversion of inventory into sales.
Overall, the JIT strategy is best suited for businesses operating in environments with stable demand patterns, reliable suppliers, and efficient production processes. It is particularly beneficial for businesses that produce perishable goods or products with short life cycles.
FAQ
The following frequently asked questions provide additional insights into the just-in-case (JIC) and just-in-time (JIT) inventory management strategies:
Question 1: What is the primary difference between JIC and JIT?
Answer: The primary difference lies in the approach to inventory management. JIC maintains a safety stock buffer to minimize the risk of stockouts, while JIT aims to eliminate waste and improve efficiency by minimizing inventory levels and producing goods only when customer demand materializes.
Question 2: When is JIC the preferred strategy?
Answer: JIC is best suited for businesses operating in environments with high demand uncertainty, unpredictable supply chains, or a strong emphasis on maintaining high customer service levels.
Question 3: When is JIT the preferred strategy?
Answer: JIT is best suited for businesses operating in environments with stable demand patterns, reliable suppliers, and efficient production processes.
Question 4: What are the benefits of JIC?
Answer: Benefits of JIC include minimizing stockouts, preserving customer satisfaction, mitigating lost sales, and maintaining market share.
Question 5: What are the benefits of JIT?
Answer: Benefits of JIT include reducing lead times, improving customer responsiveness, reducing production costs, increasing flexibility, reducing carrying costs, lowering the risk of obsolescence, and improving cash flow.
Question 6: What are the challenges of JIC?
Answer: Challenges of JIC include increased carrying costs, risk of obsolescence, and the need for accurate demand forecasting.
Question 7: What are the challenges of JIT?
Answer: Challenges of JIT include the need for precise coordination and collaboration among suppliers, manufacturers, and distributors, as well as accurate demand forecasting and efficient production planning.
Closing Paragraph for FAQ:
Ultimately, the choice between JIC and JIT depends on a careful consideration of factors such as demand patterns, supply chain reliability, cost of carrying inventory, and the level of customer service desired. Businesses should evaluate their specific circumstances and objectives to determine the most appropriate inventory management strategy.
The following section provides additional tips for effective inventory management practices.
Tips
The following practical tips can help businesses effectively implement just-in-case (JIC) and just-in-time (JIT) inventory management strategies:
Tip 1: Accurate Demand Forecasting:
Accurate demand forecasting is crucial for both JIC and JIT strategies. Businesses should invest in robust forecasting tools and techniques to better predict customer demand patterns and adjust inventory levels accordingly.
Tip 2: Supplier Collaboration and Communication:
Effective supplier collaboration and communication are essential for JIT success. Businesses should establish strong relationships with suppliers to ensure reliable and timely deliveries. Open communication is key to addressing supply chain disruptions and adjusting production schedules as needed.
Tip 3: Efficient Production Planning and Scheduling:
Efficient production planning and scheduling are critical for both JIC and JIT strategies. Businesses should optimize their production processes to minimize lead times and reduce waste. This includes implementing lean manufacturing techniques and using advanced planning and scheduling software.
Tip 4: Continuous Improvement and Performance Monitoring:
Continuous improvement and performance monitoring are essential for optimizing inventory management practices. Businesses should regularly review their inventory levels, lead times, and carrying costs to identify areas for improvement. This includes implementing quality control measures to reduce defects and improve product quality.
Closing Paragraph for Tips:
By following these tips, businesses can improve their inventory management practices, reduce costs, and enhance customer satisfaction. Effective inventory management is a key component of supply chain efficiency and overall business success.
In conclusion, JIC and JIT are two distinct inventory management strategies with different strengths and weaknesses. The choice between these strategies depends on a variety of factors, including demand patterns, supply chain reliability, and the level of customer service desired. By carefully considering these factors and implementing effective inventory management practices, businesses can optimize their inventory levels, reduce costs, and improve customer satisfaction.
Conclusion
Just-in-case (JIC) and just-in-time (JIT) are two distinct inventory management strategies that offer different approaches to optimizing inventory levels and ensuring efficient operations. JIC prioritizes maintaining a safety stock buffer to minimize the risk of stockouts, while JIT aims to eliminate waste and improve efficiency by minimizing inventory levels and producing goods only when customer demand materializes.
The choice between JIC and JIT depends on various factors, including demand patterns, supply chain reliability, the cost of carrying inventory, and the level of customer service desired. Businesses should carefully consider these factors and implement effective inventory management practices to achieve optimal inventory levels, reduce costs, and enhance customer satisfaction.
Closing Message:
Effective inventory management is a cornerstone of supply chain efficiency and overall business success. By understanding the key differences between JIC and JIT strategies and implementing appropriate inventory management practices, businesses can optimize their operations, improve customer service, and gain a competitive advantage in today's dynamic business environment.
Jenn Carter And Kyle Richh: Exploring Their Connection
Walking Dandruff Pictures Of Cheyletiella Mite Bites On Humans
Cleanest Rivers In The United States

Justin Case

Justin Case by rimax420 on DeviantArt
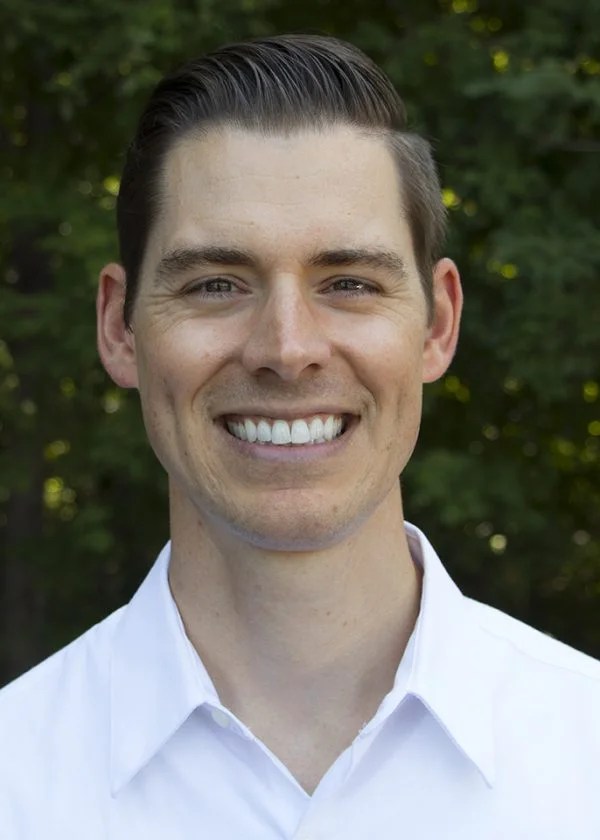
Five Questions With Justin Case Finance and Operations
ncG1vNJzZmiipaeutLXCbGWapaNoe6W1xqKrmqSfmLKiutKpmJydo2OwsLmOo6ysrJmjeqSt0p5kmqaUYre2v9OipWasmaKyb7TTpqM%3D